Aluminum Aerosol Cans Manufacturing Plant Project Report 2024: Processes, Costs and Considerations
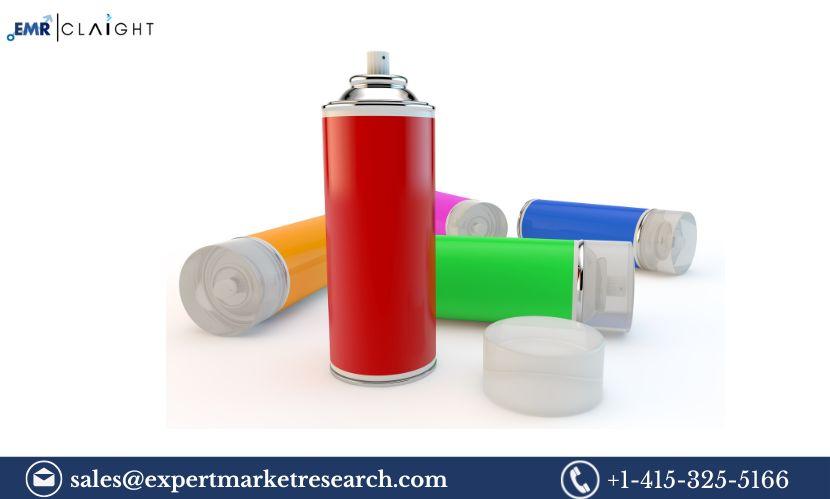
Aluminum aerosol cans have become a staple packaging solution for various consumer products, including personal care items, cosmetics, household cleaners, and industrial chemicals. These cans offer numerous advantages, such as lightweight, durability, corrosion resistance, and recyclability, making them highly preferred in the packaging industry. The demand for aluminum aerosol cans has been growing, driven by the increasing use of aerosol products in personal care, household, and industrial sectors. Setting up an aluminum aerosol cans manufacturing plant can be a lucrative business opportunity, especially with the growing global demand for environmentally friendly packaging solutions. In this article, we provide an in-depth look at an Aluminum Aerosol Cans Manufacturing Plant Project Report, covering key aspects such as the production process, raw materials, market potential, equipment, regulatory requirements, and financial considerations.
What Are Aluminum Aerosol Cans?
Aluminum aerosol cans are pressurized containers designed to hold products that are dispensed as a fine mist or spray when the valve is pressed. These cans are commonly used for products like deodorants, air fresheners, shaving creams, hair sprays, and industrial cleaners. The structure of an aluminum aerosol can consists of an aluminum body, a valve mechanism, and a cap or nozzle for dispensing the product.
The advantages of aluminum aerosol cans include:
- Lightweight: Aluminum is lightweight, making the cans easy to handle and transport.
- Durability: The material is strong and resistant to impact, ensuring the product remains protected during shipping and handling.
- Corrosion Resistance: Aluminum is resistant to rust and corrosion, ensuring the product remains safe and stable.
- Recyclability: Aluminum cans are highly recyclable, making them an environmentally friendly packaging choice.
- Efficiency: The pressurized system of aerosol cans ensures controlled dispensing and even distribution of the product.
Get a Free Sample Report with Table of Contents@
The Growing Demand for Aluminum Aerosol Cans
The demand for aluminum aerosol cans has been steadily rising due to several key factors:
-
Increasing Consumer Demand for Aerosol Products: The use of aerosol-based products in the personal care, household, and industrial sectors has expanded in recent years. Products such as deodorants, hairsprays, air fresheners, and cleaning agents are commonly packaged in aerosol cans, driving the demand for aluminum cans.
-
Rising Preference for Sustainable Packaging: Aluminum is a highly recyclable material, making aluminum aerosol cans an attractive choice for brands and consumers who prioritize sustainability. With increasing environmental awareness, companies are seeking eco-friendly packaging options, further boosting the demand for aluminum cans.
-
Growth of the Personal Care and Household Industries: The global expansion of the personal care and household products industries has led to an increased need for aerosol cans. The rising adoption of aerosol-based products in emerging markets has further contributed to the growth of this packaging solution.
-
Advancements in Aerosol Technology: Improvements in aerosol technology have made it easier to design and manufacture more efficient and durable aerosol cans. Newer valve and actuator systems enhance the performance of aerosol cans, making them even more popular for a variety of applications.
Aluminum Aerosol Can Manufacturing Process
The production of aluminum aerosol cans involves several critical steps, each of which requires precision and specialized equipment. Below is a detailed overview of the manufacturing process:
1. Raw Material Procurement
The primary raw material for manufacturing aluminum aerosol cans is aluminum sheet or aluminum coil, which is sourced from suppliers. The aluminum used for aerosol cans is typically thin, high-quality, and of a specific alloy to ensure the cans' strength, lightness, and resistance to corrosion.
2. Blanking and Shaping
The first step in the manufacturing process is blanking, where aluminum sheets are cut into circular blanks, which will later form the body of the aerosol can. These blanks are then sent through a deep-drawing machine that shapes the aluminum into a cylindrical form.
- Deep Drawing: The process of deep drawing involves pulling the blank into a mold to create the cylindrical body of the can. This process is critical for ensuring the can’s uniformity and structural integrity.
3. Necking and Trimming
Once the can's body has been shaped, the next step is necking, where the top edge of the can is reduced in diameter to create a neck. This will allow the valve to be securely attached. The necked cans are then trimmed to ensure a clean edge.
4. Internal Coating
After the basic structure of the can is formed, it is essential to apply an internal coating to protect the product inside from reacting with the aluminum. This coating also prevents corrosion, ensuring that the contents remain stable over time. The internal coating is typically sprayed or baked onto the interior surface of the can.
5. Exterior Printing and Coating
The next step is to apply the exterior design and protective coating. The can's exterior is often printed with brand logos, product information, and other details using advanced printing techniques like offset printing or screen printing. After printing, an external protective coating is applied to prevent scratching, fading, and to enhance the can's appearance.
6. Valve and Cap Fitting
The final step in the manufacturing process is the fitting of the valve and cap. The valve is the crucial component that regulates the release of the product when the user presses the can. The valve is placed at the neck of the can, and the cap is then sealed to secure the contents.
- Valve Insertion: Specialized machines are used to insert the valve into the neck of the can. This process ensures a tight seal to prevent leaks and preserve the pressurization.
7. Quality Control and Testing
Before the cans are ready for distribution, they undergo rigorous quality control checks to ensure they meet industry standards. These checks include:
- Pressure Testing: To ensure the cans can withstand the internal pressure required for aerosol dispensing.
- Leakage Testing: To detect any leaks in the cans, which could compromise the safety of the product.
- Visual Inspection: To ensure that the cans are free from defects, scratches, or printing errors.
8. Packaging and Shipping
Once the aluminum aerosol cans have passed all quality control tests, they are packaged and prepared for shipment. The cans are grouped into cartons or other containers, ready for delivery to customers in various industries.
Required Equipment for Aluminum Aerosol Cans Manufacturing Plant
Setting up an aluminum aerosol can manufacturing plant requires several essential pieces of equipment:
- Aluminum Sheet or Coil Cutting Machine: For cutting aluminum sheets into blanks.
- Deep Drawing Machine: For shaping the aluminum into cylindrical can bodies.
- Necking and Trimming Machines: For reducing the diameter of the can and trimming the edges.
- Coating Machines: For applying internal and external coatings to the cans.
- Printing Machines: For applying brand logos and product information on the cans.
- Valve Insertion Machines: For inserting the valve into the can’s neck.
- Leak and Pressure Testing Equipment: For ensuring the quality and safety of the cans.
- Packaging Machines: For packing the finished cans into cartons.
Regulatory Considerations
When setting up an aluminum aerosol can manufacturing plant, it is essential to comply with several regulatory standards:
- Environmental Regulations: Proper waste management and the use of eco-friendly materials are essential. Compliance with local and international environmental standards is required to ensure that the plant operates sustainably.
- Health and Safety Regulations: Due to the use of pressurized cans and potentially hazardous chemicals in the production process, strict safety protocols must be followed to protect workers and ensure safe operations.
- Quality Standards: The cans must meet international quality standards (e.g., ISO certifications) and specific industry requirements related to food safety, pharmaceutical products, or cosmetics, depending on the target market.
Market Potential and Industry Outlook
The aluminum aerosol can market is expected to continue expanding in the coming years due to the growing demand for aerosol-based products. Key industries driving this demand include:
- Personal Care and Cosmetics: Products like deodorants, hairsprays, and shaving creams are commonly packaged in aerosol cans, contributing to the market’s growth.
- Household Products: Items such as air fresheners, insecticides, and cleaning agents are often packaged in aluminum aerosol cans.
- Pharmaceutical and Industrial Applications: Aerosol cans are used for medical sprays, lubricants, paints, and industrial cleaners.
The increasing demand for sustainable and recyclable packaging also makes aluminum aerosol cans an attractive option for manufacturers, further boosting their popularity in various sectors.
Financial Feasibility and Investment Considerations
Setting up an aluminum aerosol can manufacturing plant involves significant initial investment and ongoing operational costs. The following factors must be considered when evaluating the financial feasibility of the project:
- Initial Capital Investment: The costs of acquiring land, machinery, raw materials, and plant construction.
- Operating Costs: These include labor, raw materials, utilities, and maintenance costs.
- Revenue Generation: Revenue depends on production capacity, customer demand, and market pricing for aerosol cans.
- Profit Margins: The profit margins will depend on efficient production processes, material costs, and pricing strategies.
A detailed financial analysis should be included in the project report to ensure the plant’s viability and profitability.
FAQs
1. What are aluminum aerosol cans used for?
Aluminum aerosol cans are used to package products like deodorants, hairsprays, air fresheners, shaving creams, and industrial cleaners. They are designed to dispense the product as a fine mist when the valve is pressed.
2. What are the main materials used in the production of aluminum aerosol cans?
The main material used is aluminum sheet or coil, which is shaped and coated to create the can. Other materials include the valve, cap, and coatings for the interior and exterior of the can.
3. What industries use aluminum aerosol cans?
Industries such as personal care, household products, pharmaceuticals, automotive, and industrial applications use aluminum aerosol cans for packaging.
4. What are the regulatory requirements for aluminum aerosol can manufacturing?
Manufacturers must comply with environmental, health, and safety regulations, as well as quality standards such as ISO certifications, to ensure safe and sustainable production.
5. How much does it cost to set up an aluminum aerosol can manufacturing plant?
The cost of setting up an aluminum aerosol can manufacturing plant depends on factors such as the scale of production, machinery, raw materials, and infrastructure. A detailed financial analysis is required to determine the exact investment needed.
Related Reports
https://www.expertmarketresearch.com.au/reports/australia-automotive-camera-market
https://www.expertmarketresearch.com.au/reports/australia-automotive-pneumatic-actuators-market
https://www.expertmarketresearch.com.au/reports/australia-carbon-black-market
Media Contact:
Company Name: Claight Corporation
Contact Person: Lewis Fernandas, Corporate Sales Specialist — U.S.A.
Email: sales@expertmarketresearch.com
Toll Free Number: +1–415–325–5166 | +44–702–402–5790
Address: 30 North Gould Street, Sheridan, WY 82801, USA
Website: www.expertmarketresearch.com
Aus Site: https://www.expertmarketresearch.com.au
- Auto, moto
- Catering
- Leisure, entertainment
- Animals
- Beauty, health
- Education, tutors
- Sports and coaches
- Construction and repair
- Products and stores
- Tourism and recreation
- Finance and Insurance
- Literature
- Music
- History
- Politics
- Religion
- Art
- Movie
- Theater
- Wellness
- Accessories
- Business
- Various