Ceramic Tiles Manufacturing Plant Project Report: Production Setup and Market Analysis
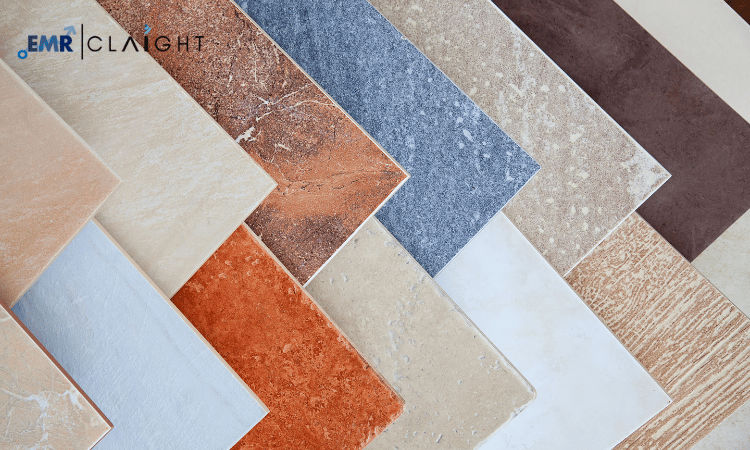
Ceramic tiles are a popular building material used in residential, commercial, and industrial spaces due to their durability, versatility, and aesthetic appeal. These tiles are made from natural materials like clay and sand and are available in various designs, colours, and finishes, making them suitable for floors, walls, and other surfaces. With increasing urbanisation and the growth of the construction industry, the demand for ceramic tiles has surged globally. Establishing a ceramic tiles manufacturing plant presents a lucrative opportunity to cater to this expanding market while meeting the needs of diverse industries.
Overview of Ceramic Tiles
Ceramic tiles are thin, flat slabs made from a mix of natural materials, primarily clay, sand, and minerals, which are shaped and then fired at high temperatures. These tiles are known for their strength, resistance to moisture, and ease of maintenance. They come in a variety of forms, including glazed, unglazed, matte, and glossy finishes, and are commonly used for flooring, wall cladding, and decorative purposes.
Get a Free Sample Report with Table of Contents@ https://www.expertmarketresearch.com/prefeasibility-reports/ceramic-tiles-manufacturing-plant-project-report/requestsample
Key Components of a Ceramic Tiles Manufacturing Plant
-
Raw Material Procurement
The primary raw materials for ceramic tile production include clay, feldspar, sand, and kaolin. High-quality raw materials are essential to ensure the durability and aesthetic appeal of the tiles. Securing reliable suppliers and maintaining quality checks are critical for consistent production. -
Machinery and Equipment
Advanced machinery is necessary for efficient production and quality control. Key equipment includes mixers, presses, kilns, glazing machines, and polishing units. Automated systems help streamline processes, reduce wastage, and improve precision in manufacturing. -
Plant Layout and Design
A well-planned layout ensures smooth workflow and optimal utilisation of space. The design should accommodate machinery, storage areas, and workspaces while adhering to safety and environmental standards. Proper ventilation and dust management systems are also essential. -
Utilities and Infrastructure
Adequate utilities such as electricity, water, and gas are critical for operations. Reliable power supply is essential for running high-temperature kilns and other machinery. Water is required for mixing raw materials, glazing, and cooling processes. -
Workforce and Training
Skilled personnel are needed to operate machinery, oversee production, and ensure quality control. Regular training programs help workers stay updated on the latest technologies and safety protocols, enhancing efficiency and reducing errors.
Manufacturing Process of Ceramic Tiles
The production of ceramic tiles involves several stages, each designed to achieve the desired quality and finish:
-
Raw Material Preparation
Raw materials such as clay, feldspar, and sand are crushed, ground, and mixed to form a homogenous blend. The mixture is then moistened to create a workable mass. -
Forming
The prepared mixture is shaped into tiles using pressing or extrusion methods. The tiles are then dried to remove excess moisture and ensure dimensional stability. -
Firing
The dried tiles are fired in kilns at high temperatures to harden and strengthen them. This step enhances the durability and resistance of the tiles. -
Glazing and Decoration
For glazed tiles, a layer of liquid glaze is applied to the surface before a second firing. Decorative designs can also be added during this stage, providing the tiles with their final appearance. -
Polishing and Finishing
The fired tiles are polished and cut to the desired dimensions. Quality checks are conducted to ensure consistency and compliance with industry standards. -
Packaging and Storage
The finished tiles are packed in sturdy materials to protect them during transportation and storage. Proper labelling ensures easy identification and handling.
Applications of Ceramic Tiles
Ceramic tiles are highly versatile and cater to various applications across different sectors:
- Residential Spaces: Widely used in homes for flooring, walls, and kitchen backsplashes due to their durability and aesthetic appeal.
- Commercial Buildings: Ceramic tiles are a preferred choice for offices, malls, and hotels because of their ease of maintenance and wide range of designs.
- Industrial Settings: These tiles are used in factories and warehouses for their resistance to chemicals, stains, and heavy foot traffic.
- Outdoor Spaces: Anti-slip ceramic tiles are ideal for patios, terraces, and swimming pool areas.
- Decorative Uses: Ceramic tiles are also used in murals, mosaics, and other artistic applications to enhance the visual appeal of spaces.
Market Potential and Demand Drivers
The growing demand for ceramic tiles can be attributed to several factors:
-
Urbanisation and Infrastructure Development
Rapid urbanisation and government initiatives in infrastructure development have increased the use of ceramic tiles in construction projects. -
Rising Disposable Income
Higher disposable income has led to increased spending on home improvement and renovation, boosting the demand for ceramic tiles. -
Aesthetic Preferences
Consumers are increasingly opting for stylish and customised tiles to enhance the look of their spaces, driving innovation in tile designs and finishes. -
Durability and Low Maintenance
The long-lasting nature and easy maintenance of ceramic tiles make them a cost-effective choice, further increasing their popularity.
Challenges in Ceramic Tiles Manufacturing
-
Raw Material Quality
Inconsistent raw material quality can affect the durability and finish of the tiles. Regular quality checks and reliable sourcing help mitigate this challenge. -
Energy Consumption
The production process, especially firing in kilns, consumes significant energy, impacting operational costs. Investing in energy-efficient machinery can address this issue. -
Competition
The ceramic tile market is highly competitive, with numerous players offering a wide range of products. Differentiation through quality, design, and innovation is crucial for success. -
Environmental Regulations
Compliance with environmental standards, especially concerning emissions and waste management, can be challenging but is essential for sustainable operations.
Sustainability in Ceramic Tiles Manufacturing
The ceramic tiles industry is increasingly adopting sustainable practices to reduce its environmental impact. Key initiatives include:
- Energy Efficiency: Using advanced kilns and machinery to lower energy consumption.
- Recycling: Incorporating recycled materials into the production process to minimise waste.
- Water Management: Implementing systems for water recycling and efficient usage.
- Eco-Friendly Products: Developing tiles with lower environmental footprints, such as those made from natural or recycled materials.
Key Success Factors for a Ceramic Tiles Manufacturing Plant
- Product Quality: Consistent quality in design, strength, and finish is essential to meet customer expectations and build brand reputation.
- Innovation: Offering unique designs, textures, and finishes can help manufacturers stand out in a crowded market.
- Operational Efficiency: Streamlining processes and reducing wastage contribute to cost savings and higher profitability.
- Market Insights: Understanding consumer preferences and market trends enables manufacturers to offer relevant products and stay competitive.
- Sustainability Practices: Adopting eco-friendly measures enhances the brand’s appeal and ensures compliance with regulatory standards.
By focusing on these aspects, a ceramic tiles manufacturing plant can successfully cater to the growing demand for high-quality and aesthetically appealing tiles across various industries.
- Auto, moto
- Catering
- Leisure, entertainment
- Animals
- Beauty, health
- Education, tutors
- Sports and coaches
- Construction and repair
- Products and stores
- Tourism and recreation
- Finance and Insurance
- Literature
- Music
- History
- Politics
- Religion
- Art
- Movie
- Theater
- Wellness
- Accessories
- Business
- Various