Magnesium Arsenite Manufacturing Plant Project Report: Cost Analysis, Production Process, and Market Trends
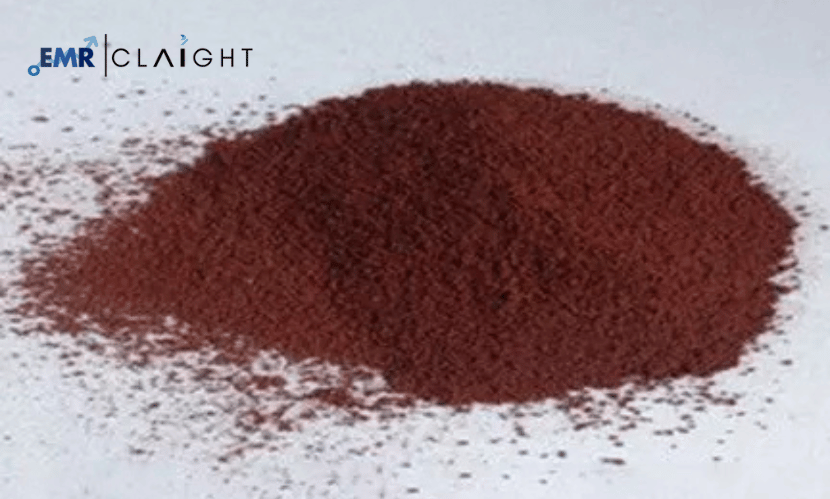
Magnesium arsenite is a niche chemical compound with unique properties and applications in specialised industries, including agricultural chemicals, research, and specialised manufacturing. Setting up a magnesium arsenite manufacturing plant involves detailed planning, a thorough understanding of the chemical properties, and an adherence to stringent safety and environmental regulations. This article explores the critical aspects of establishing such a plant, including the key processes, infrastructure requirements, and challenges, providing a comprehensive guide for stakeholders and investors.
Overview of Magnesium Arsenite Production
Magnesium arsenite is typically synthesised through chemical reactions involving magnesium compounds and arsenic-based reactants. The process requires precision to ensure the product’s purity and consistency. Due to its specialised nature, magnesium arsenite production demands advanced manufacturing systems and adherence to strict quality standards. Its applications often require tailored formulations, making it an essential compound for niche markets.
Get a Free Sample Report with Table of Contents@ https://www.expertmarketresearch.com/prefeasibility-reports/magnesium-arsenite-manufacturing-plant-project-report/requestsample
Essential Components of the Manufacturing Plant
A magnesium arsenite manufacturing plant comprises various critical components, ensuring seamless production while meeting quality and safety standards. Key elements include:
-
Raw Material Storage:
- Secure storage facilities for magnesium compounds and arsenic-based chemicals, ensuring protection from moisture and contamination.
- Proper labelling and segregation to avoid cross-contamination.
-
Reaction Units:
- Specialised reactors designed to handle arsenic-containing materials, equipped with corrosion-resistant materials.
- Systems for precise temperature and pressure control to optimise the reaction.
-
Filtration and Purification Systems:
- Advanced filtration units to separate impurities from the final product.
- Purification systems that enhance the quality and usability of magnesium arsenite.
-
Environmental Safety Systems:
- Effluent treatment units to manage liquid waste effectively.
- Air filtration systems to minimise emissions of potentially hazardous substances.
-
Packaging and Storage Units:
- Facilities for secure packaging of magnesium arsenite to maintain its stability.
- Warehouses with controlled environments to ensure product longevity.
Step-by-Step Guide to Magnesium Arsenite Production
-
Site Selection and Plant Layout:
- Choose a location with access to raw materials and utilities, along with provisions for waste management.
- Design the plant layout to maximise efficiency and safety.
-
Procurement of Equipment:
- Source high-quality reactors, filtration systems, and storage units designed to handle hazardous materials.
- Collaborate with trusted suppliers for durable and efficient machinery.
-
Installation and Commissioning:
- Assemble the plant’s components as per the layout.
- Conduct commissioning tests to ensure systems are operational and compliant with safety norms.
-
Raw Material Procurement:
- Establish reliable supply chains for magnesium and arsenic compounds, ensuring consistent quality.
- Verify raw material specifications through rigorous quality checks.
-
Production Process Execution:
- Initiate the synthesis process under controlled conditions, closely monitoring parameters like temperature, pressure, and reaction time.
- Collect and process the product using filtration and purification systems.
-
Quality Assurance:
- Test the final product for purity, composition, and performance parameters.
- Address deviations promptly to maintain product standards.
Applications of Magnesium Arsenite
Magnesium arsenite serves various specialised applications due to its chemical properties. Some prominent uses include:
-
Agricultural Chemicals:
- Utilised in the formulation of specific pesticides and soil treatment agents.
- Provides targeted solutions for managing certain agricultural challenges.
-
Research and Development:
- A key component in experimental setups in chemistry and material sciences.
- Offers unique properties for studying arsenic interactions and applications.
-
Specialised Manufacturing:
- Used in producing niche industrial products that require arsenic-based additives.
- Plays a role in creating compounds with enhanced functionality.
Safety and Environmental Considerations
Due to the presence of arsenic, magnesium arsenite production involves inherent risks. A responsible approach to safety and environmental management is crucial:
-
Waste Management:
- Install effluent treatment plants to neutralise arsenic-containing waste before disposal.
- Adopt practices to recycle and reuse waste materials where feasible.
-
Emission Control:
- Use advanced scrubbers and filters to minimise air emissions.
- Conduct regular monitoring to ensure compliance with environmental norms.
-
Worker Safety:
- Provide comprehensive training for workers handling hazardous materials.
- Equip personnel with protective gear and ensure adherence to safety protocols.
Operational Challenges
Setting up and managing a magnesium arsenite manufacturing plant comes with several challenges, such as:
-
Regulatory Compliance:
- Navigating stringent environmental and safety regulations.
- Ensuring periodic audits and certifications to maintain operational licences.
-
Raw Material Availability:
- Securing a reliable supply of arsenic compounds amidst fluctuating market dynamics.
- Maintaining cost-effective procurement channels.
-
Technological Demands:
- Investing in advanced equipment to ensure precision and quality.
- Adapting to technological advancements to stay competitive.
Emerging Trends in Magnesium Arsenite Manufacturing
The industry is witnessing shifts towards more sustainable and efficient practices. Key trends include:
-
Green Chemistry Initiatives:
- Emphasis on reducing the environmental footprint through eco-friendly production methods.
- Development of alternative processes that minimise hazardous waste.
-
Automation and AI Integration:
- Adoption of smart manufacturing practices for enhanced control and efficiency.
- Use of AI to optimise production parameters and reduce human error.
-
R&D Investments:
- Increased focus on exploring new applications for magnesium arsenite.
- Collaboration between industries and research institutions to innovate and expand the market.
Economic and Social Impact
A magnesium arsenite manufacturing plant contributes to the economy and society in several ways:
-
Employment Opportunities:
- Generates jobs for skilled and semi-skilled workers in the production facility and allied industries.
-
Boost to Local Economy:
- Promotes regional development through infrastructure investments and procurement of local resources.
-
Global Market Presence:
- Positions manufacturers to cater to international markets, enhancing foreign exchange earnings.
By addressing operational challenges and embracing innovation, magnesium arsenite manufacturing plants can establish themselves as key players in the chemical industry while ensuring sustainable and responsible growth.
- Авто, мото
- Кейтеринг
- Досуг, развлечения
- Животные
- Красота, здоровье
- Образование, репетиторы
- Спорт и тренеры
- Строительство и ремонт
- Товары и магазины
- Туризм и отдых
- Финансы и страхование
- Литература
- Музыка
- История
- Политика
- Религия
- Искусство
- Кино
- Театр
- Хорошее здоровье
- Аксессуары
- Бизнес
- Разное